abgeschlossene
Projekte
Phase 2

Das am Fraunhofer IWU entwickelte High-Speed 3D-Druckverfahren SEAM (Screw Extrusion Additiv Manufacturing) weist eine extrem gesteigerte Prozessgeschwindigkeit bei der Verarbeitung von günstigem Standard-Kunststoffgranulat auf. Zur additiven Herstellung von lastpfadangepassten hoch belastbarer Strukturbauteilen ist die Erweiterung des Verfahrens mit einer Endlosfaserverarbeitung vorgesehen. Ziel des Vorhabens war daher die Entwicklung einer an das bestehende Extrusionssystem adaptierbaren Düse, zum Einzug und Imprägnierung eines trockenen Kohlenstofffaserrovings mit der Kunststoffschmelze.
Im Verlauf der Projektarbeiten wurde so ein Imprägnierwerkzeug entwickelt, das den besonderen Anforderungen im Kunststoff-3D-Druck, wie minimalem Gewicht und Abmessungen gerecht wird. Mittels externer und interner Faserspreizung wird eine gute Benetzung der Einzelfasern mit der thermoplastischen Matrix erzielt. Durch ein rotierendes Ventil kann die Schmelze bedarfsgerecht reguliert und zugeschalten werden. Das System spielt insbesondere dort seine Stärken aus, wo lediglich lokale Verstärkungen aufzubringen sind. Neben den gedruckten, meist kurzfaserverstärkten Teilen aus dem High-Speed 3D-Druckverfahren SEAM kann hierbei auch der Einsatz von flächigen oder extrudierten Halbzeugen genannt werden.
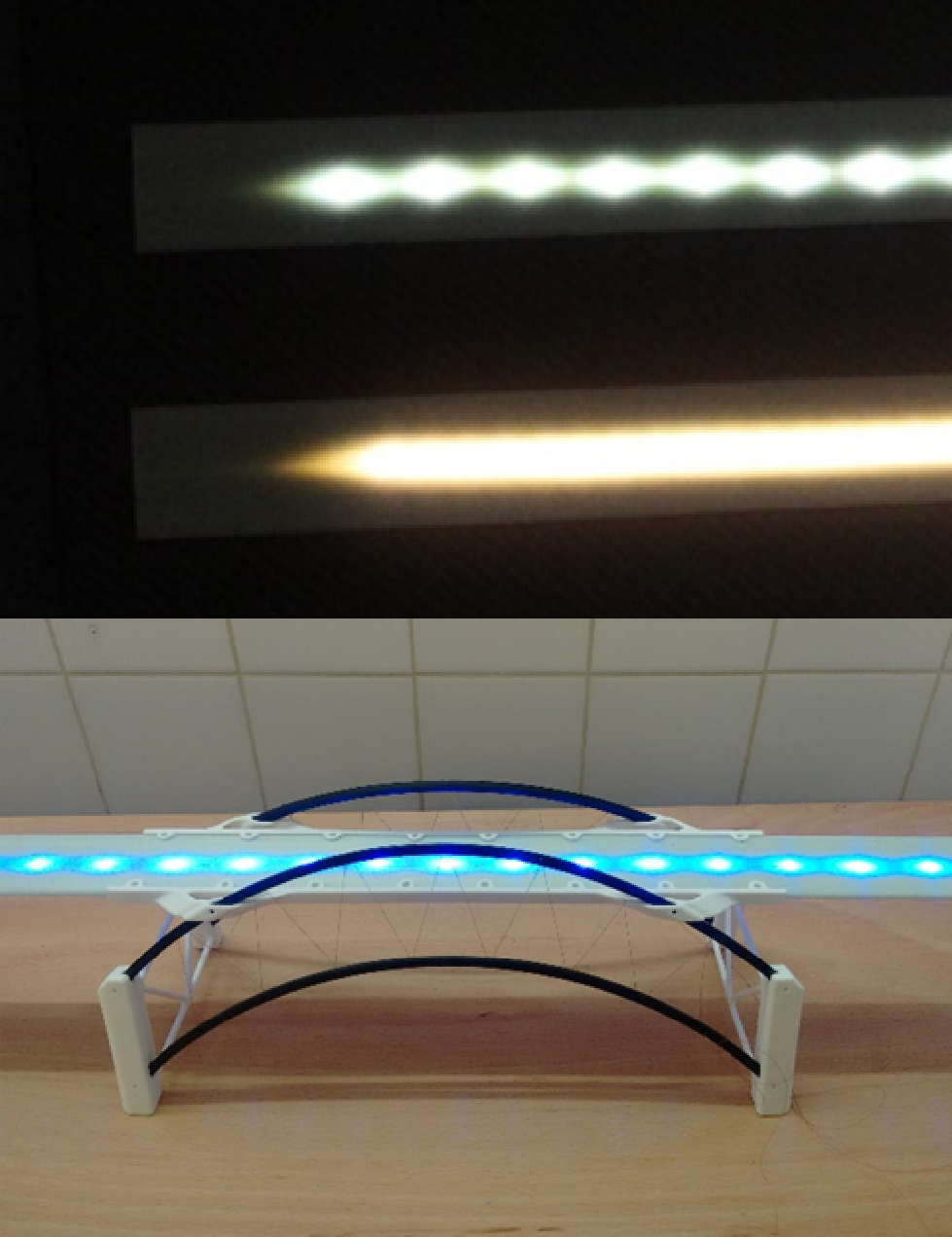
Für komplexe Profilstrukturen wird der Einsatz faserverstärkter Kunststoffprofile aufgrund deren herausragender Eigenschaften angestrebt. Der Leichtbaugrad kann durch gezielten Einsatz von endlosfaserverstärkten Kunststoffen und über Funktionsintegration in vielen Bereichen erhöht werden. Hierfür sind serientaugliche Prozesse wie die Pultrusion und der 3D-Druck für individuellere Lösungen geeignet. Endlosfaserverstärkte Pultrusionsprofile (gerade oder gekrümmt) können entsprechend der Anforderungen an den Querschnitt und die mechanische Belastbarkeit durch die Auswahl geeigneter Materialien und Faserausrichtungen optimal ausgelegt und hergestellt werden. Zusätzlich können verschiedene Funktionen, wie Sensorik, Beleuchtung oder weitere in das Profil integriert werden. Dies ermöglicht zum Beispiel eine Zustandsüberwachung.
Verschiedene Elemente zur Funktionalisierung wurden erfolgreich mittels Pultrusion in den Profilen eingebracht und auf ihre Funktion überprüft darunter:
- Zustandsüberwachung über integrierte, statt aufgeklebte Sensoren (Dehnung / Temperatur, Feuchtigkeit etc.)
- Designelemente durch Beleuchtung z. B. mittels LEDs
- Funktionselemente (Touchsensor z. B. nutzbar als Schalter etc.)
- Integration von Heizelementen
Vorteile im Vergleich mit dem Stand der Technik:
- Integrierte, statt nachträgliches Aufkleben der Funktionselemente
- Mögliche Kombination mit 3D gedruckten Schnittstellen, angepasst auf spezifische Anforderungen
- Reinigung der Oberflächen problemlos möglich, die Funktionselemente stellen keine Störstelle dar
- Schutz vor äußeren Einflüssen (Umgebungsbedingung, Manipulation)
Des Weiteren wurden Untersuchung zu Kontaktierungsvarianten durchgeführt, für welche derzeit eine Patentanmeldung geprüft wird.
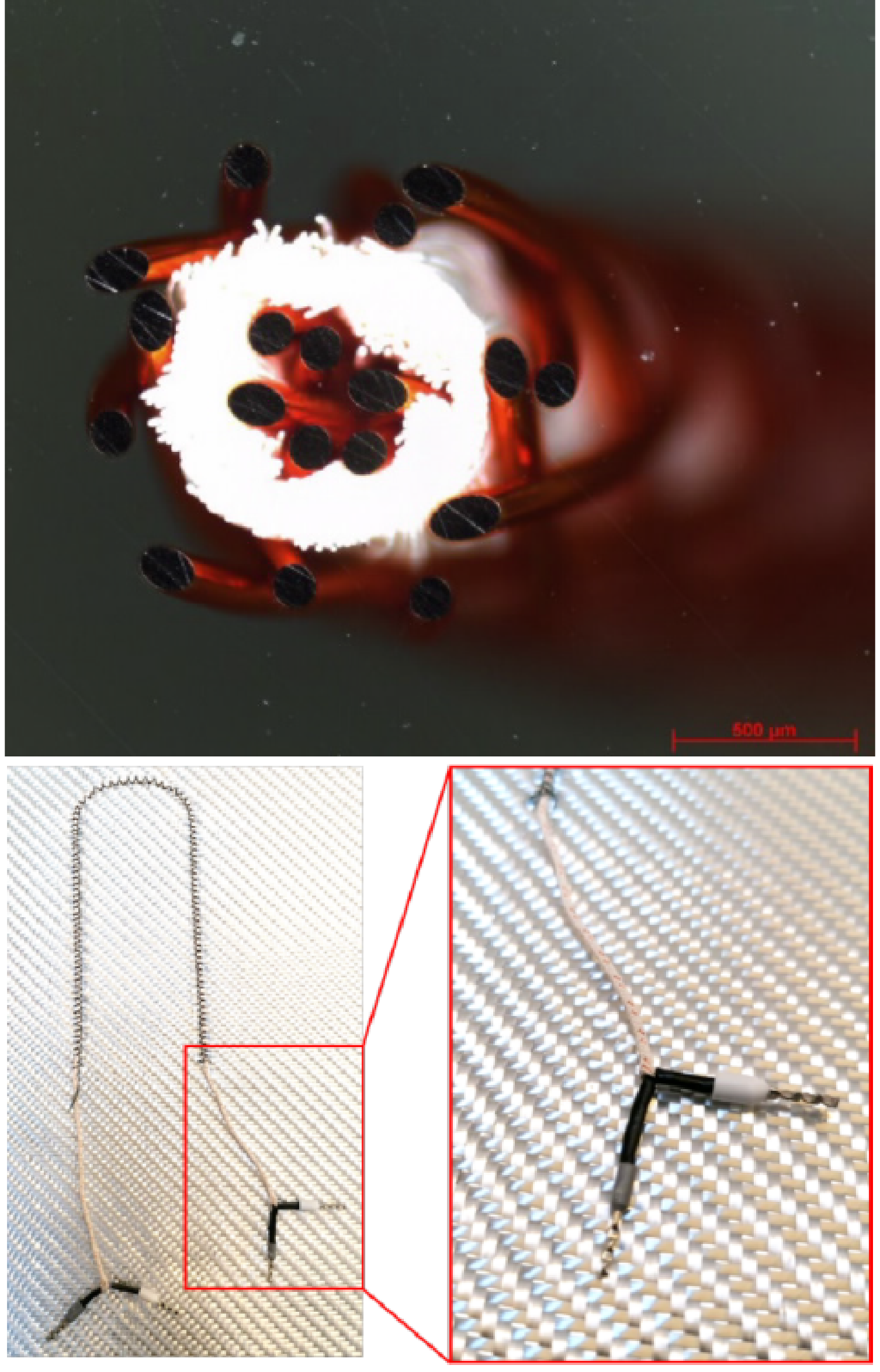
Herstellung von schmelzgesponnenen thermoplastischen Piezogarnen
Piezoelektrische Aktivität in extremer Formvielfalt in Kunststoffkörper und Textilien einzubringen, ist die Vision dieses Projektes. Dazu werden thermoplastische Verbundwerkstoffe mit piezoelektrischen Partikeln entwickelt, die mit dem bekannten „Fused Filament Fabrication“-Verfahren verdruckt oder zu flexiblen textilen Fasern versponnen werden. Nach Aktivierung der piezoelektrischen Eigenschaften mittels neuentwickelter Polungstechnologien und Kontaktierung der piezoelektrisch aktiven Bereiche liegen so lokale sensorische und aktorische Eigenschaften vor.
Mit der Bereitstellung dieser neuartigen Garnkonstruktionen und zugehörigen Technologien können eine Vielzahl neuer Anwendungsfelder insbesondere mit Fokus auf deren sensorische Überwachung zur Zustands- bzw. Belastungsanalyse erschlossen werden. Hierzu zählen Bereiche mit Fokus auf textilbasierte Leichtbaulösungen, wie Maschinenbau, Fahrzeugbau, Robotik, Architektur, Orthetik und Prothetik.
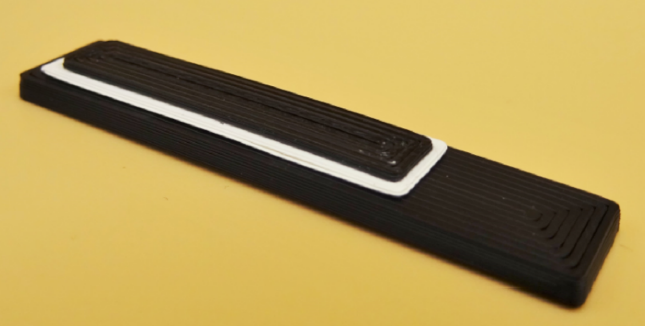
Additive Fertigungsverfahren wie etwa das Fused Filament Fabrication (FFF) erlauben die Herstellung komplexer Geometrien. Gepaart mit neuartigen Funktionsmaterialien können diesen Strukturen Eigenschaften verliehen werden, die völlig neue Anwendungsfelder erschließen können. Die gedruckte piezoaktive Zwischenschicht wurde im Projekt entwickelt und ist umgeben von elektrisch leitfähigem PLA. Somit können sensorische als auch aktorische Funktionen in thermoplastischen Bauteilen übernommen werden.
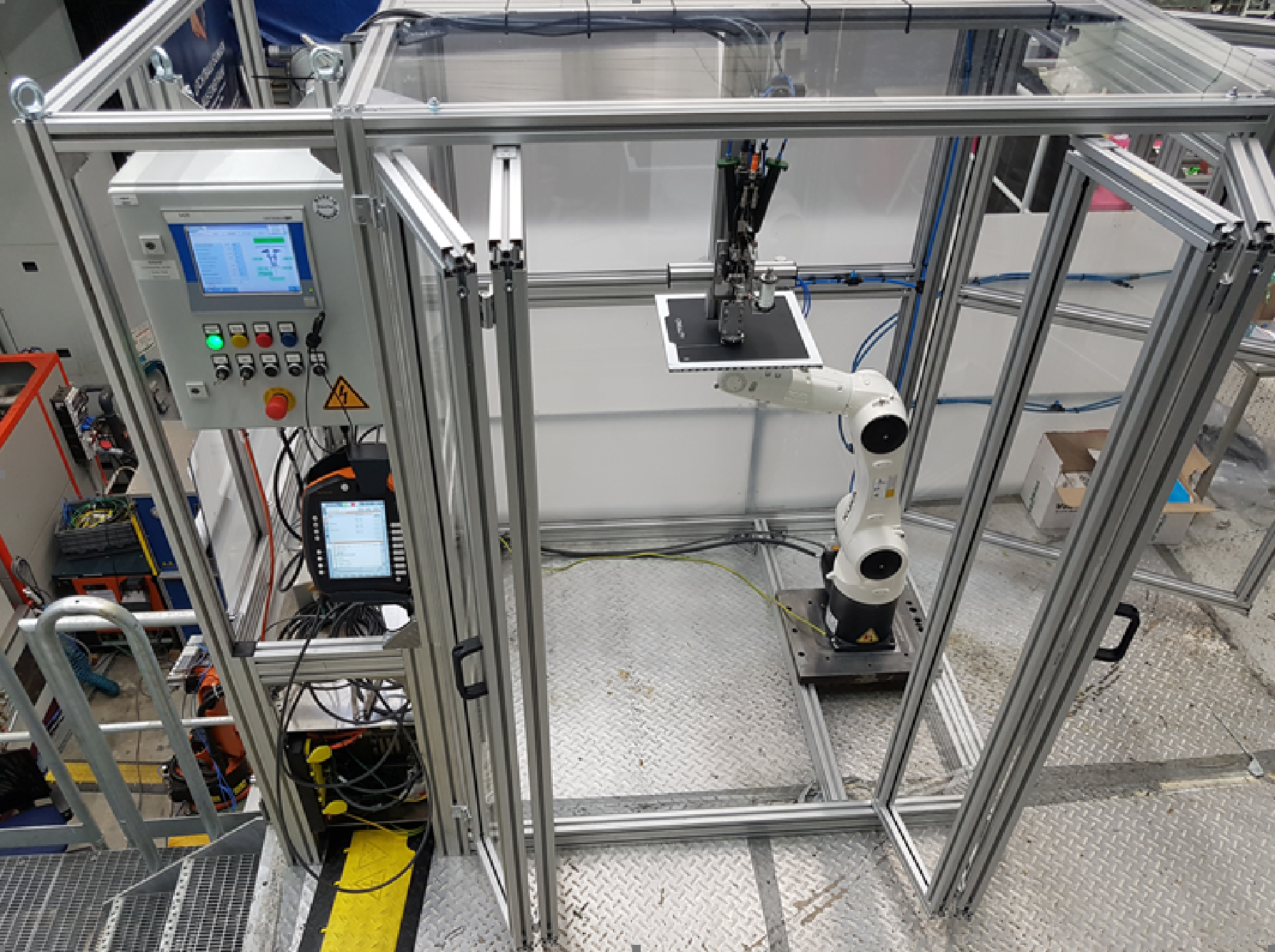
Individualisierte Leichtbaustrukturen auf Basis endlosfaserverstärkter Kunststoffe mit maßgeschneiderten Eigenschaften sowie beanspruchungsgerecht optimierter Geometrie sind mit konventionellen Technologien nur eingeschränkt umsetzbar. Insbesondere duroplastische Matrixsysteme bieten hierbei ein breites Verarbeitungsspektrum zur gezielten Einstellung einer stufenweisen Vernetzungsreaktion. Ziel des Projektes ist die additive Fertigung faserverstärkter, duroplastischer 3D-Druck-Strukturen mit lokal variierbaren Eigenschaften. Der hierzu entwickelte Verarbeitungsprozess beruht auf den Schritten Imprägnierung eines endlosen Faserfilaments (Roving) mit dem Reaktionsharz, Belichtung des lichthärtenden Harzes zur Aktivierung eines Photoinitiators und der nachfolgenden Faserablage. Die im Projekt 3D³ realisierte automatisierte Fertigungszelle ermöglicht den 3D-Druck von ein oder zwei-komponentigen Matrixsystem mit Endlosfaserverstärkung, indem der imprägnierte Faserstrang auf ein robotergeführtes Druckbett unter dem neuartigen, stationären Druckkopf abgelegt wird. Eine durch UV-Strahlung initiierte Aushärtereaktion in Kombination mit einer thermischen Nachhärtung ermöglicht die flexible Einstellung der lokalen Verbundeigenschaften. Die Abstimmung der Prozessparameter Belichtungszeit und -intensität sowie der Druckgeschwindigkeit ist entscheidend für reproduzierbar hohe Verbundqualitäten in Verbindung mit einer hohen Imprägniergüte der eingebrachten Faserverstärkungen. Das entwickelte Verfahren ist für die Herstellung von individualisierten Bauteilen mit hohen Anforderungen an die thermo-mechanischen Eigenschaften bei kleinen Losgrößen konzipiert.
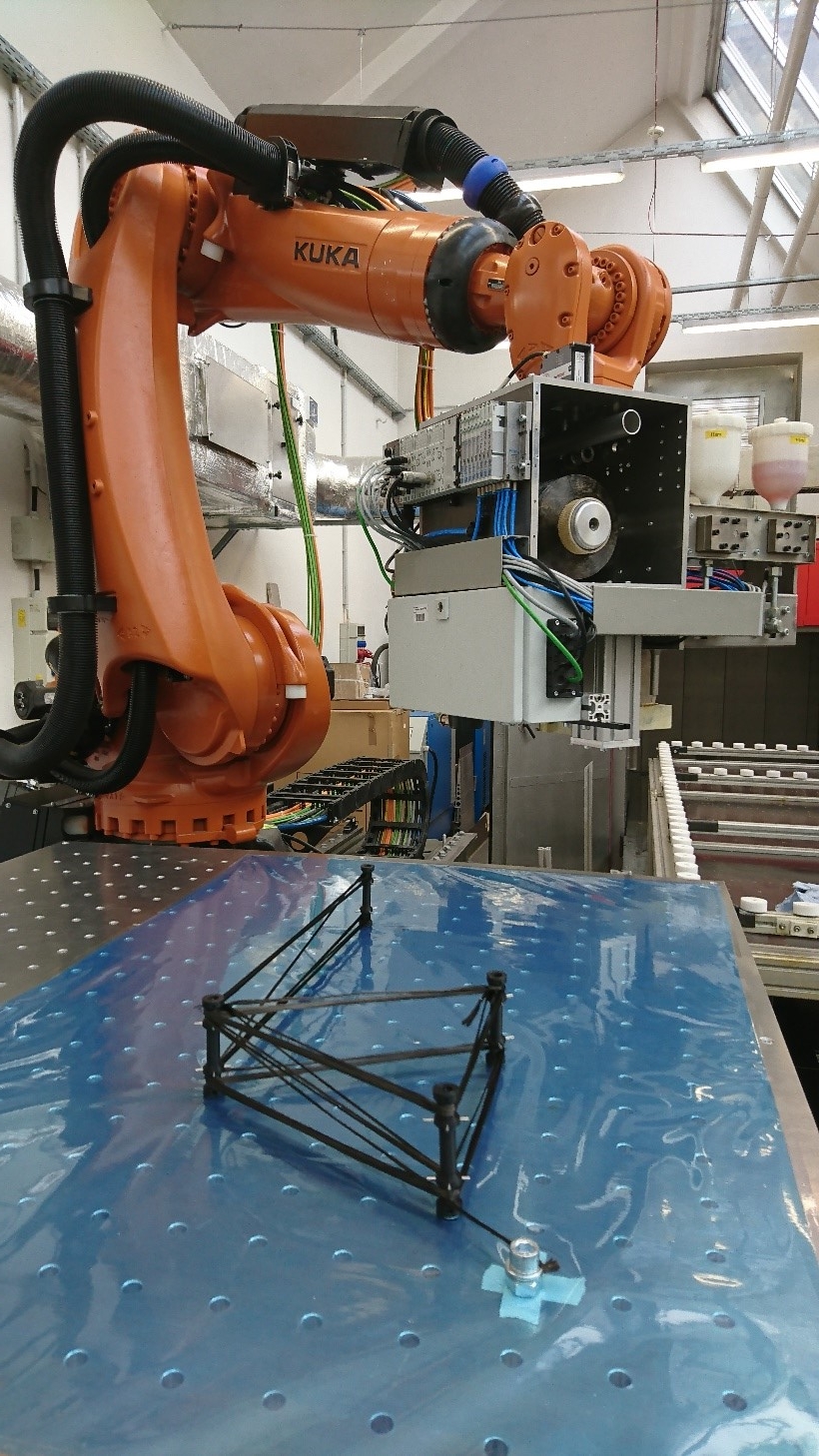
Im Rahmen des Projektes wurden basierend auf einer simulationsgestützten Auslegung hochkomplexe adaptive 3D-FKV-Strukturen entwickelt und durch eine gezielte räumliche, robotergestützte Ablage von Formgedächtnislegierungen (FGL) und vorimprägnierten Verstärkungsfasern umgesetzt. Derartige komplexe Leichtbaustrukturen mit Formvariabilität ermöglichen komplett neuartige kosten- und gewichtsminimierte Umsetzungsvarianten für eine Vielzahl an Produkten in diversen Branchen. Hierzu zählen u. a.:
- Automatisierungstechnik (z. B. robotische Industriegreifer),
- Medizintechnik (z. B. aktive Handprothesen),
- Fahrzeugbau (z. B. adaptive Klappen und Flügelsystem zur aktiven Beeinflussung des Strömungsverhaltens und schaltbare Feder-/ Dämpferelemente) und
- Energietechnik (z. B. adaptive Flaps für Windkraft-Rotorblätter zur Effizienzsteigerung bzw. zur Geräuschminimierung).
Um diese Zielstellung zu erreichen, wurden die am ITM bestehenden FEM-Modelle im Hinblick auf die neuen Anforderungen erweitert und auf dieser Basis systematisch die Verformungspotenziale von FKV-Strukturen in Abhängigkeit ihrer geometrischen sowie strukturellen Parameter virtuell analysiert und evaluiert. Es wurden Systeme zur effektiven Ankopplung der FGL-Aktoren an die umgebenden FKV-Strukturen entwickelt und deren Eignung sowohl theoretisch analysiert als auch praktisch funktionsseitig erprobt und bewertet, um eine Vorzugslösung auszuwählen. Zur Fertigung der Strukturen wurden robotergestützte Prozesse zur lastgerechten Fadenablage und Inline-Imprägnierung um Möglichkeiten zur gezielten sequenziellen dreidimensionalen Ablage von Verstärkungsgarnen (Kohlenstoff- bzw. Glasfasern) und FGL erweitert, siehe Abbildung 1.
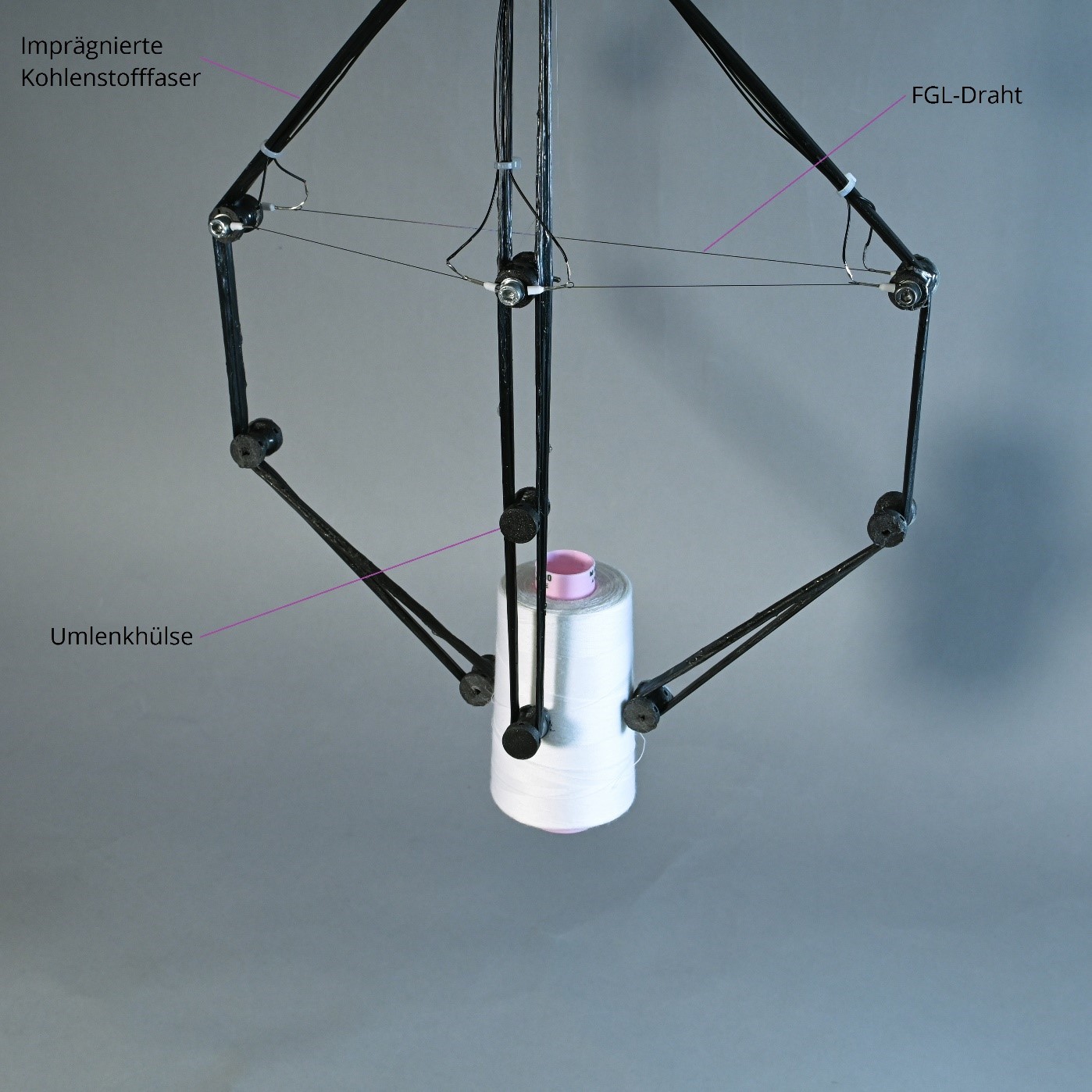
Die entwickelten Teilprozesse und Technologien wurden zu einer Prozesskette zusammengeführt und die erreichbare Bauteilqualität anhand von Probekörpern validiert. Das Funktionspotenzial des neuartigen robotergestützten Garnablageverfahrens zur simultanen Verarbeitbarkeit von imprägnierten Verstärkungsfäden und drahtförmigen FGL-Aktoren wurde anhand eines generischen Funktionsdemonstrators in Form eines 3-Fingergreifers aufgezeigt (Abbildung 2).
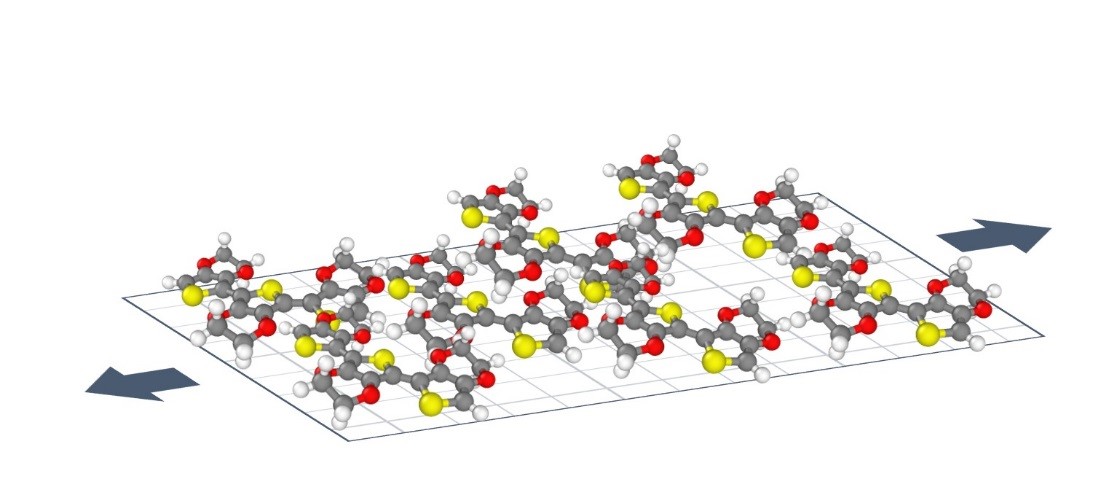
Eine der Herausforderungen für additiv gefertigte Strukturen liegt in der Vorhersage und Erhöhung ihrer Lebensdauer, für die in situ Messmethoden zu Erfassung spezifischer Beanspruchungen erforderlich sind. Die komplexen Geometrien topologieoptimierter Bauteile schließen jedoch die Anwendung der meisten herkömmlichen Verfahren, wie Dehnungsmessstreifen zur Beobachtung lokaler Deformationen, aus.
Auf Basis multifunktionaler und multimaterieller Druckmethoden wird es in Zukunft möglich sein, die Generierung entsprechender Sensoren in den Druckprozess mit einzubeziehen. In diesem Projekt sollen die ersten Schritte hin zu einer bedarfsgerechten Sensorik für additiv gefertigte Strukturen unternommen werden. Dazu werden funktionalisierte Oberflächen simuliert, die den Beanspruchungszustand lokal und in situ ermitteln. Die gewonnenen Erkenntnisse werden im Anschluss für eine Optimierung am Beispiel von gedruckten Metallstrukturen hinsichtlich ihrer Belastbarkeit eingesetzt.
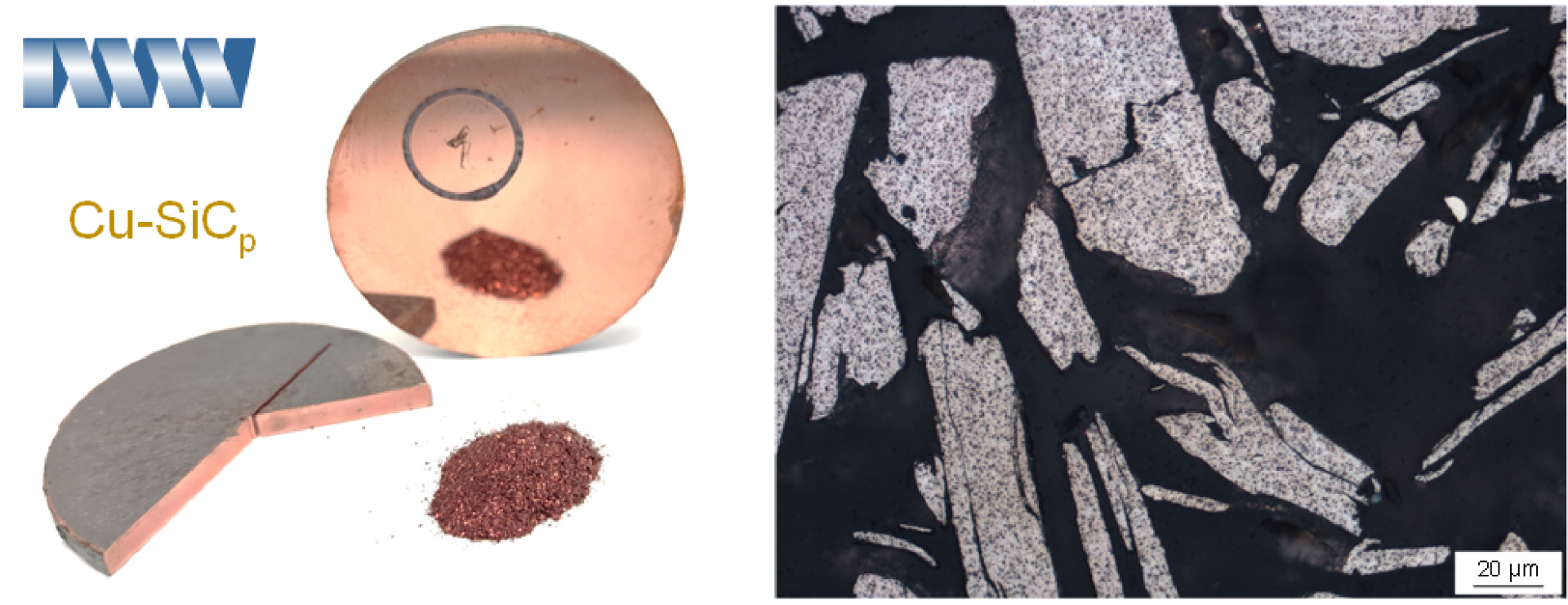
In dem Projekt wurden maßgeschneiderte metallische Pulver auf Basis von Kupfer mit einer Partikelverstärkung entwickelt. Schon seit vielen Jahren ist die Professur auf die Herstellung derartiger Verbundpulver spezialisiert, die durch einen Mahlprozess in Hochenergiekugelmühlen entstehen. Mit den Verbundpulvern stehen neue Ausgangsmaterialien für additive Fertigungsverfahren, wie Binder Jetting oder selektives Laserschmelzen zu Verfügung, die bisher nicht kommerziell verfügbar sind. Kompakte Materialien aus dem Verbundpulver, die im Projekt über feldunterstütztes Sintern (FAST/SPS) hergestellt wurden, weißen eine deutlich höher Härte und verbesserte Verschleißeigenschaften als das reines Kupfer oder gleicharte Pulvergemische auf. Das Zufügen weiterer Legierungskomponenten oder Additive im Mahlproesse erlaubt zudem eine hohe Flexibilität in der chemischen Zusammensetzung der Pulver. Auch die Übertragung auf andere Matrixwerkstoff wie Aluminium und Titan ist möglich. Bitte Fragen Sie uns bei Interesse nach Ihrem maßgeschneiderten Verbundpulver.
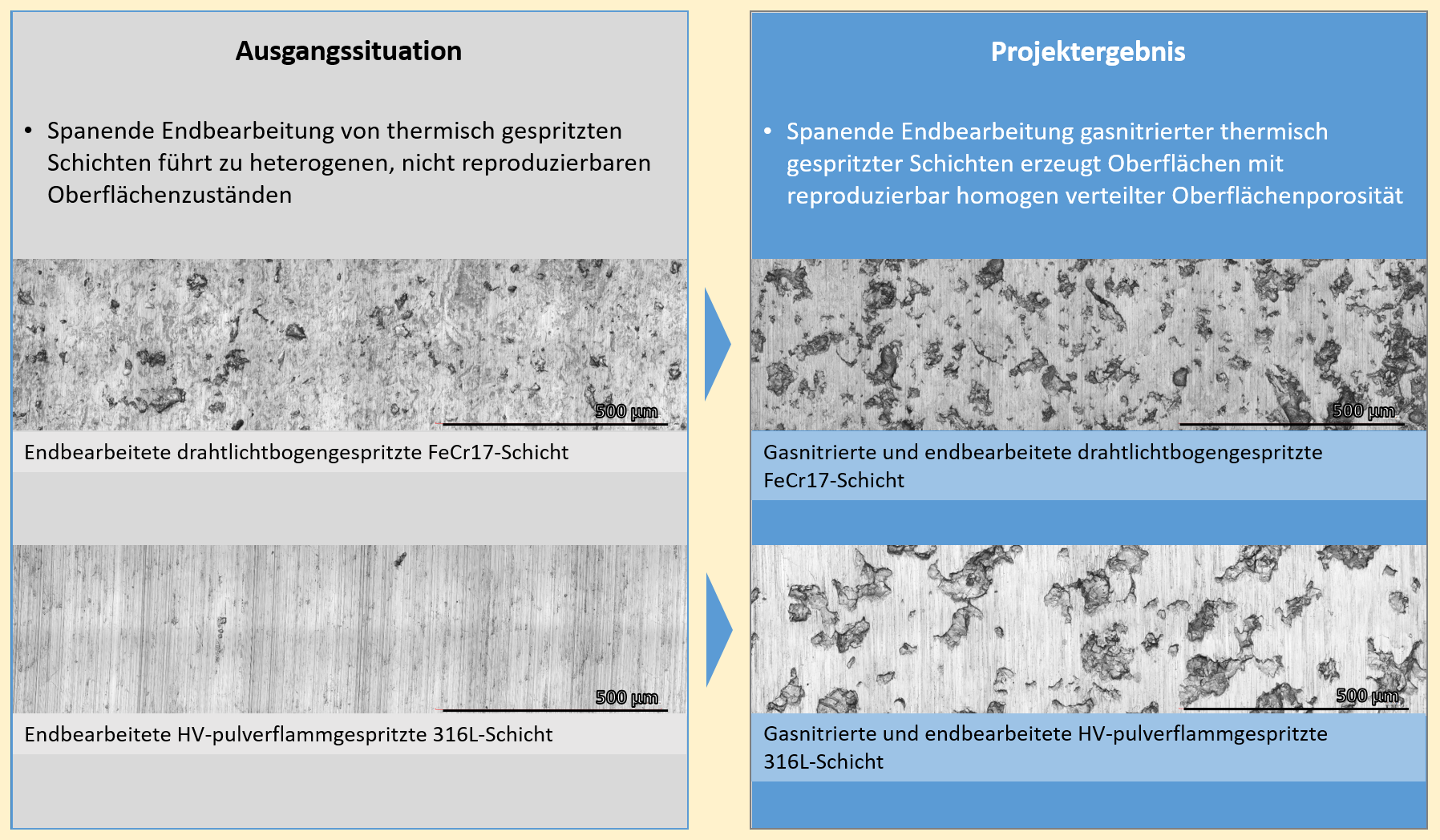
Thermisch gespritzte Schichten werden u.a. im Maschinen- und Anlagenbau sowie im Werkzeug- und Formenbau angewendet. Geforderte Einsatzeigenschaften stehen dabei häufig im Zusammenhang mit der Feingestalt der Bauteiloberflächen. Beispielsweise werden für Oberflächen in tribologischen Systemen häufig definierte Ölrückhaltevolumina gefordert, um Notlaufeigenschaften sicherzustellen. Die Finishbearbeitung beeinflusst somit die Tribologie von Gleitsystemen, den entstehenden Bauteilverschleiß, thermische Effekte im Bauteilbetrieb, die Eigenschaften eingreifender Werkstoffoberflächen und vieles mehr. Sie muss deshalb einerseits an die Zielanwendung angepasst sein, andererseits zu reproduzierbaren Ergebnissen in Bezug auf die geometrischen und werkstofflichen Oberflächeneigenschaften führen.
Im Projekt wurden durch die Kombination von Hartdrehen bzw. Hartfräsen mit vorangestelltem Gasnitrieren die offenporigen thermisch gespritzten Schichten in einen gewünschten und robust reproduzierbaren Oberflächenzustand überführt. Die Zielgrößen der Bearbeitung betreffen gleichermaßen die mikroskalige Oberflächentopographie, d.h. Rauheit und oberflächenoffene Porosität, als auch den mikrostrukturellen und chemischen Zustand der oberflächennahen Randzonen der endbearbeiteten Bauteile.
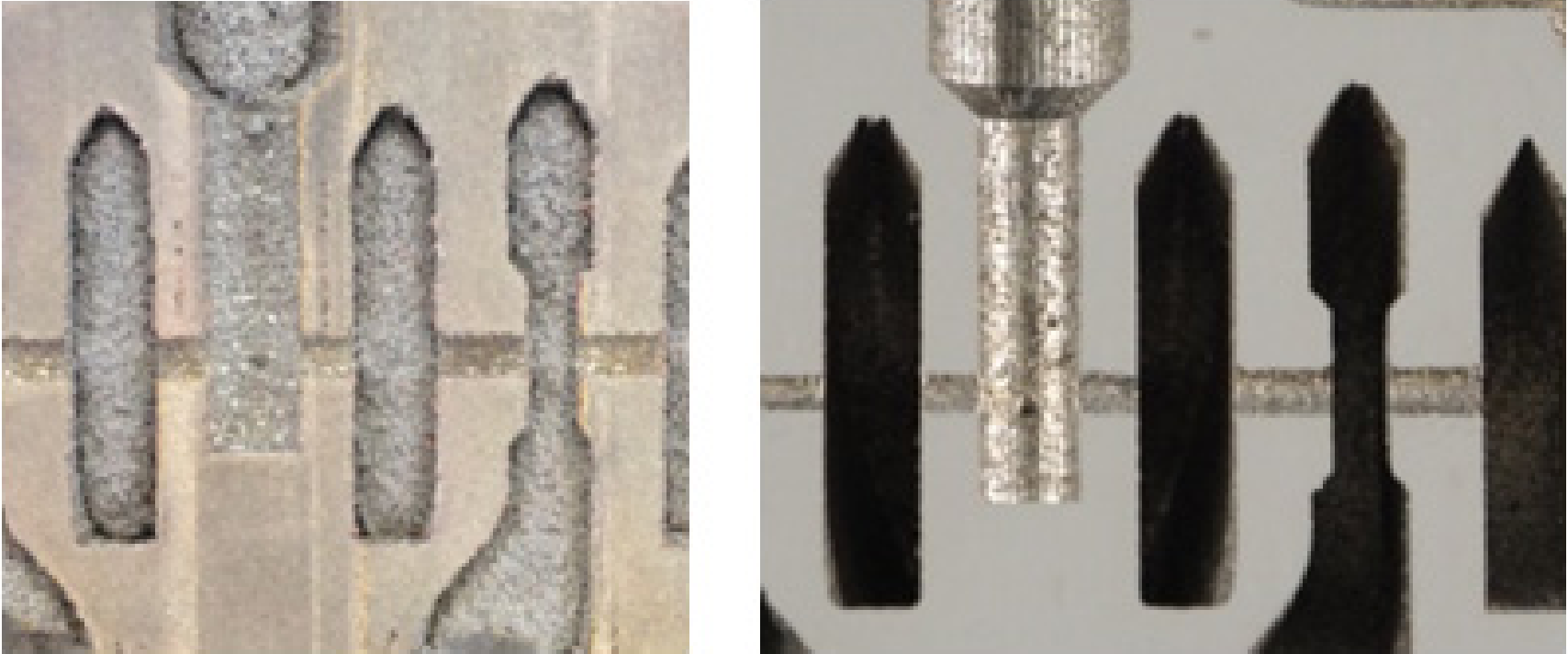
In der industriellen Fertigung zeichnet sich über die letzten Jahre ein stetig wachsender Bedarf an hochflexiblen Fertigungsverfahren ab. Diese Entwicklung ist mit einem ebenso stetigen Anstieg des geometrischen und materialtechnischen Anforderungsprofils einzelner Bauteile gekoppelt, so dass die additive Fertigung zunehmend an Relevanz gewinnt. Der wirtschaftlich rentable Einsatz dieser Verfahren wird momentan jedoch noch durch viele Herausforderungen in Bezug auf die Materialvielfalt, Prozessgeschwindigkeit und insbesondere Präzision begrenzt. Häufig ist eine Nachbearbeitung durch trennende Fertigungsverfahren notwendig. Mit Hilfe elektrochemischer Abtragprozesse soll in diesem Projekt ein Ansatz für eine teilautomatisierte Endbearbeitung komplexer Innengeometrien additiv gefertigter metallischer Bauteile entwickelt werden. Dabei wird die Prozesskette durch den Einsatz des Elektrochemischen Abtragens (Electrochemical Machining – ECM) zeitlich und wirtschaftlich effizient gestaltet. Dieses Verfahren soll insbesondere bei komplexeren Innengeometrien mit variierenden Querschnitten, Bohrungsverschneidungen oder Hinterschneidungen angewandt werden, da diese bislang nicht lokal nachbearbeitet werden können.
Ziel des Projekts war die Entwicklung einer effizienten Fertigungstechnik zur automatisierten Feinbearbeitung von additiv gefertigten Werkzeugformen.
Innerhalb des Projektzeitraums wurde mit Hilfe bereits entwickelter flexibler Schleifwerkzeuge eine kraft- und zeitgeregelte Prozessführung für die Finishbearbeitung gefräster Bauteile entwickelt. Die Beschreibung der parameterseitigen Zusammenhänge in einem Prozessmodell bildet dafür die Grundlage. Anhand exemplarischer Werkzeuggeometrien wurde die Prozesskette: Additive Fertigung, Fräs- und Finishbearbeitung untersucht und Potentialfelder der einzelnen Arbeitsschritte analysiert. Mit Hilfe der adaptiven Nacharbeit konnten, besonders im Bereich der Fräsbearbeitung, deutliche Reduzierungen der Bearbeitungsdauer gegenüber konventionellen Prozessketten nachgewiesen werden. Die additive Fertigung von Werkzeugstahl 1.2709 mittels Selektiven Laserschmelzens (SLS) stellt dabei im Bereich kleiner Werkzeugkomponeten oder für die hybride Teilefertigung ein attraktives Verfahren dar.
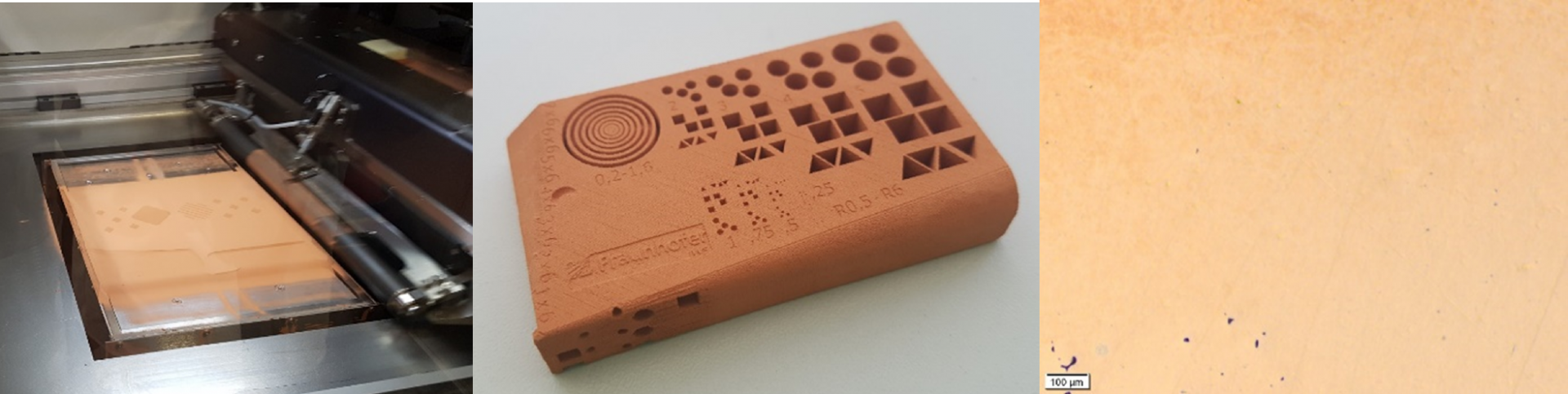
Ziel des Vorhabens ist die Verarbeitung von Kupfer mittels des additiven Fertigungsverfahrens namens Binder Jetting zu komplexen Geometrien und Bauteilen, wie Spulen oder Wärmetauscher. Kupfer besitzt aufgrund seiner herausragenden Eigenschaften (elektrische Leitfähigkeit, Wärmeleitung, Duktilität) eine riesige industriell-wirtschaftliche Bedeutung. Heute ist dieses Material in der gesamten Elektrobranche unverzichtbar.
Insbesondere hinsichtlich der Dichtheit von additiv gefertigten Volumenkörpern besteht großer Forschungsbedarf. Die gefertigten Teile weisen zumeist nur eine geringe Dichte von ~ 85 % nach dem Sintern auf, da der organische Binder als gasförmiges Produkt abtransportiert werden muss. Weiterhin ist die Verunreinigung des Bauteils mit Kohlenstoff nicht ganz auszuschließen.
Durch die Verwendung einer speziellen Pulverzusammensetzung konnte die Sinterdichte auf 97 % gesteigert werden. Die elektrische Leitfähigkeit beträgt bei dieser Sinterdichte 85 % IACS (International Annealed Copper Standard).
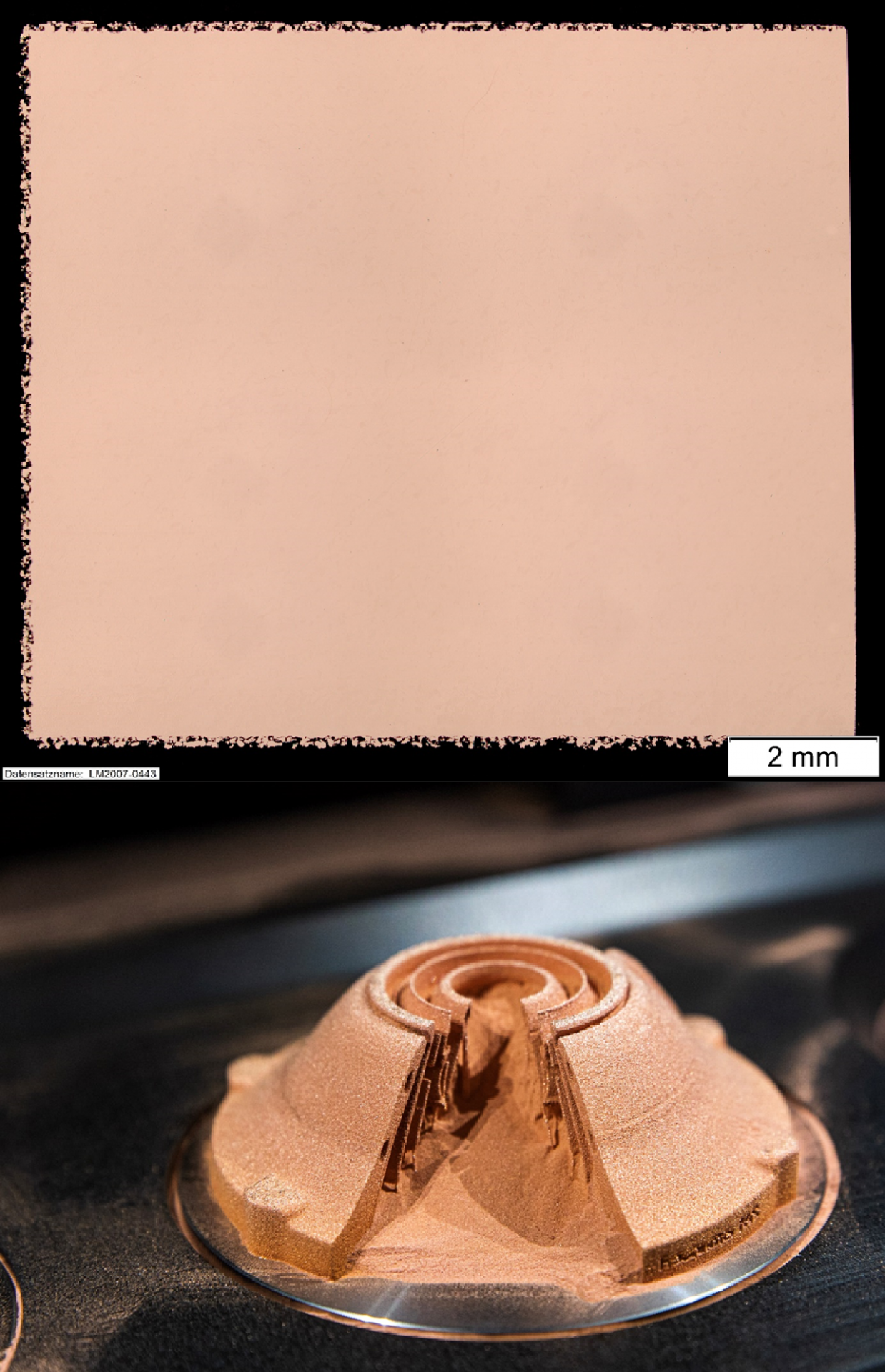
Mit der neuen Anlagentechnik, einer Maschine zum pulverbettbasierten Laserstrahlschmelzen (LPBF) mit integriertem grünen Laser der Wellenlänge 515 nm, konnte ein stabiler Prozess für den Aufbau dichter Volumenkörper aus Reinkupfer entwickelt werden mit einer relativen Dichte von 99,95 %. Außerdem wurden die elektrischen und mechanischen Materialeigenschaften ermittelt. Die elektrische Leitfähigkeit der generierten Bauteile erreichte 100 %IACS. Mit diesem Projektergebnis können nun komplexe Reinkupferbauteile mit exzellenten Eigenschaften hergestellt werden wie zum Beispiel individualisierte Induktorspulen oder Wärmetauscher für die Leistungselektronik.
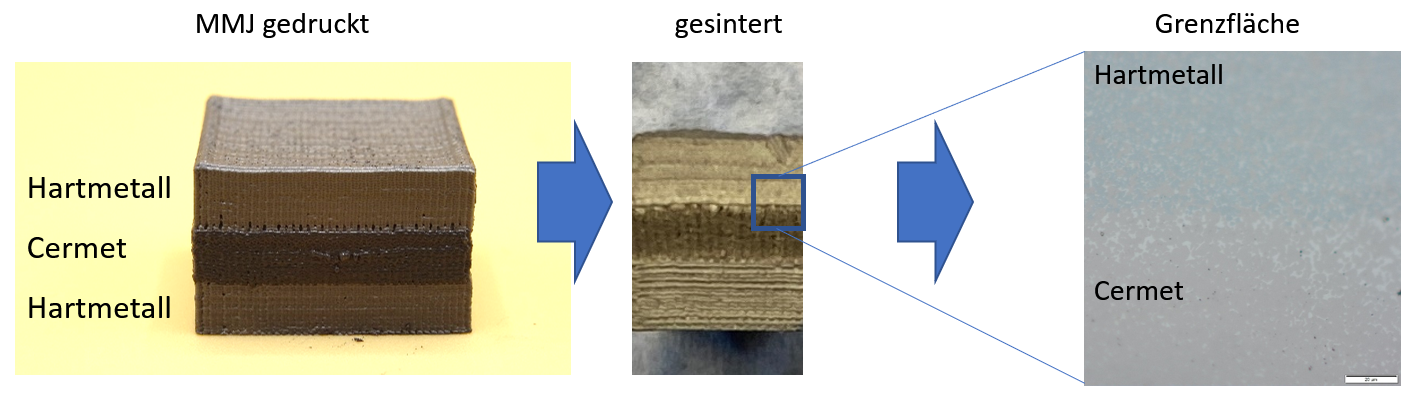
Im Projekt HardPrint sollten Funktionsgenerierungen von Werkzeugwerkstoffen der Materialklassen Hartmetall und Cermets mittels zweistufigen thermoplastischen 3D-Druck realisiert werden. Das Ziel sollte es sein, Metall-Keramik-Verbundwerkstoffe zu neuartigen innovativen Werkzeugen für Anwendungen im Bereich der Zerspanung und Oberflächenbearbeitung sowie für Verschleißanwendungen nutzbar zu machen. Als Kombinationsmöglichkeiten sollten so z.B. Werkzeuge mit stark wärmeleitfähigen Hartmetall und schwach wärmeleitfähigen Cermet realisiert oder die hohe Bruchzähigkeit von Hartmetallen mit der hohen Zunderbeständigkeit von Cermets kombiniert werden, um zukünftig auch bei Hochtemperaturzerspanungsaufgaben längere Werkzeugstandzeiten zu realisieren.
Durch eine gezielte Anpassung der Zusammensetzung konnte die Schwindung des Hartmetalls und des Cermets sehr genau aufeinander abgestimmt werden. Bei der Anpassung des thermischen Ausdehnungskoeffizient (TAK) konnte eine Anpassung bis auf < 2*10-16 (1/K) erfolgen. Das Multi-Material-Jetting (MMJ) von ausgewählten Zusammensetzungen war erfolgreich und es konnten erste einfache Beispielbauteile im Projekt generiert werden. Nach einer optimierten Sinterung konnten vollständig dichte Multimaterialbauteile hergestellt werden. An der Grenzfläche wurde keine Delaminationen festgestellt, was eine ausreichende Anpassung der Schwindung und des TAK beweist. In auf dem Projekt aufbauenden Projekten mit der Industrie sollen nun komplexere Geometrien realisiert werden

Besondere technische Herausforderungen bestehen in der additiven Fertigung keramischer Komponenten dann, wenn mehrere keramische Werkstoffe zu einem komplexen funktionalen Gebilde strukturiert und integriert werden sollen. Hierauf konzentriert sich das Teilprojekt SPM-14. Additiv gefertigte dielektrische Komponenten werden mit keramikkompatiblen funktionellen Schichten bedruckt, diese durch thermische Nachbehandlung verdichtet und so keramikbasierte Mikrosysteme mit integrierter elektrischer oder sensorischer Funktion hergestellt. Das Vorhaben konzentriert sich auf mikrofluidische Anwendungen. Neben Fragen der Werkstoffentwicklung und der Formgebungstechnologie, werden ebenso solche des Entwurfs und der funktionsbezogenen Charakterisierung der mikrofluidischen Demonstratoren und Komponenten bearbeitet.
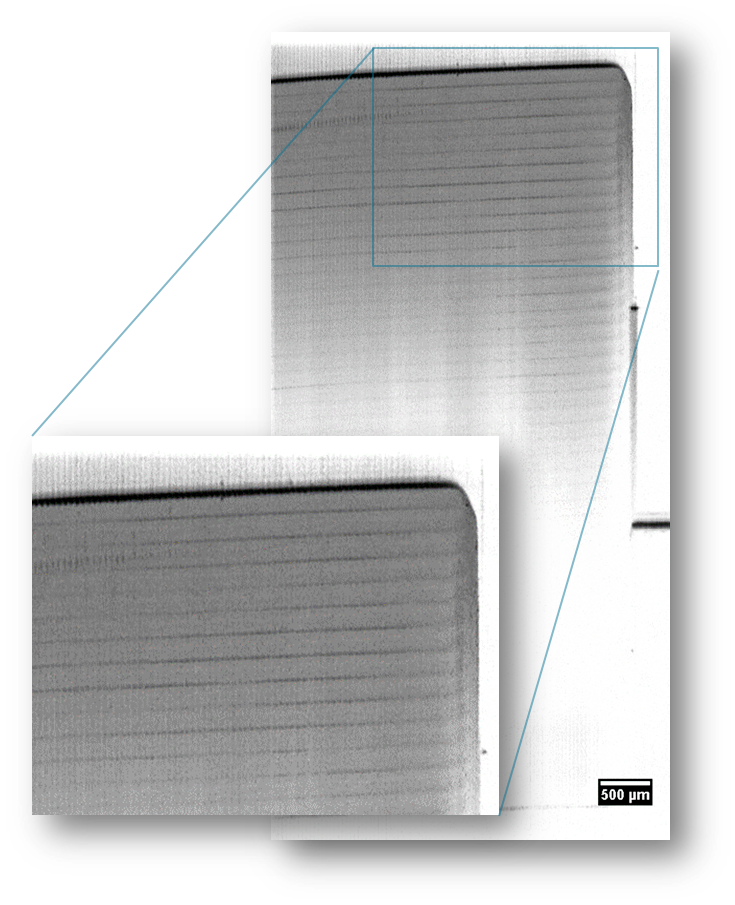
Mit diesem Vorhaben soll die optische Kohärenztomografie (OCT) in verschiedene additive Fertigungsprozesse integriert werden. Hierzu werden aus den am Fraunhofer IKTS vorhandenen keramischen AM-Verfahren drei anwendungsrelevante Verfahren evaluiert. Für diese wird neben notwendigen Qualifizierungskörpern auch ein Versuchsstand aufgebaut, der automatisiert Querschnittsbilder während des Herstellungsprozesses aufnimmt, und diese mit Hilfe von µCT-Daten der Probekörper evaluiert. Ziel ist es, Prüfkörper für die OCT zu entwickeln, die während des Prozesses mitgedruckt werden können und eine integrierte Prozessüberwachung ermöglichen.
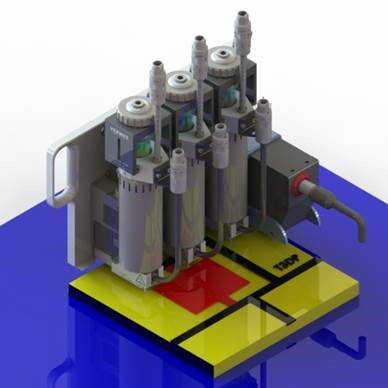
Die Entwicklung des additiven Fertigungsverfahres Thermoplastic 3D Printing (CerAM T3DP) steht vor der Herausforderung sehr komplexe prozessimmanente Zusammenhänge des Verfahrens zu ermitteln, um sowohl eine qualitätsgerechte als auch eine wirtschaftliche Fertigung ermöglichen zu können. Die Komplexität resultiert einerseits aus der Vielzahl an Einflussgrößen (aus Material, Druckprozess und Umgebung) und andererseits aus der Mehrstufigkeit des Prozesses (Drucken, Entbindern, Sintern, Nachbearbeiten). Aus der Möglichkeit, Multimaterialbauteile generieren zu können, resultiert ein zusätzlicher Komplexitätsanstieg. Für die effiziente Generierung des Prozessverständnisses und die künftige qualitätsgerechte und reproduzierbare Prozessführung werden neuartige Methoden benötigt. Ziel des Projekts ist es daher, die Potenziale von Verfahren des Data Mining und des Maschinellen Lernens zu analysieren und für den Druckprozess anzuwenden. Dabei steht die Tropfen- und Schichtbildung im Fokus der Untersuchungen.
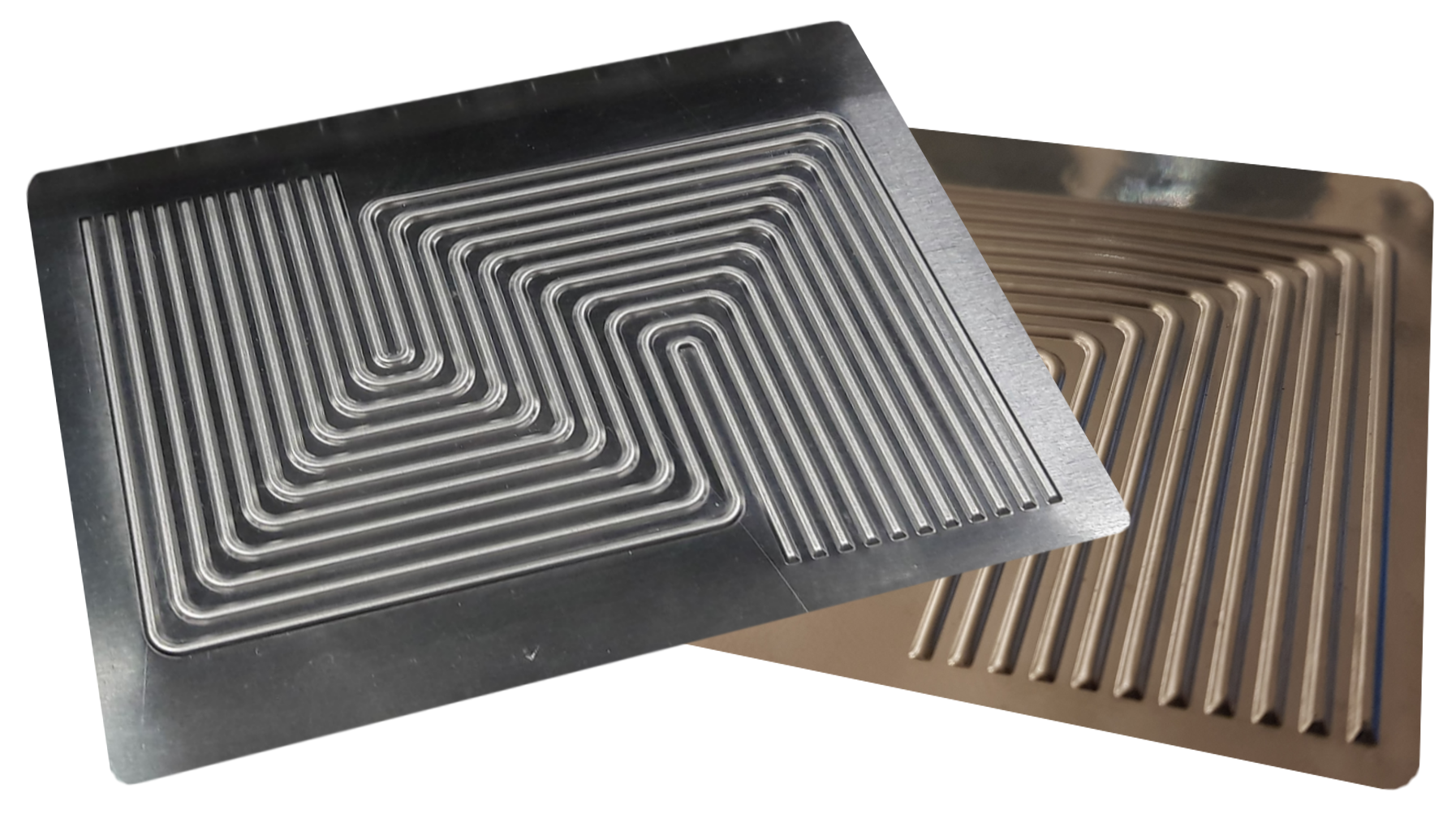
Ziel des Projektes war die Untersuchung wirkmedienbasierter Verfahren hinsichtlich ihrer Anwendbarkeit für die Fertigung von Bipolarplatten. Dabei wurde im Besonderen der Einfluss der Umformgeschwindigkeit und des verwendeten Wirkmediums betrachtet. Als Wirkmedien dienten Elastomere und HFA-Emulsionen. Die Umformung erfolgte entweder quasistatisch über konventionelle Antriebe oder über ein elektromagnetisch beschleunigtes Werkzeug. Es stellte sich heraus, dass HFA-Emulsionen wesentlich besser geeignet sind um die feinen Geometrien umzuformen. Zudem zeigte sich, dass sowohl konventionelle Antriebe als auch elektromagnetisch beschleunigte Antriebe gut für die Bauteilfertigung geeignet sind.Kontakt

Projektziel war es, Möglichkeiten zur Datenauswertung spektraler Messdaten mit Methoden des maschinellen Lernens und neuronaler Netze zu evaluieren. Systemseitig wurden dafür Prozessmessdaten mithilfe eines miniaturisierten MEMS-Nahinfrarotspektrometers gewonnen und hinsichtlich der Konzentration an Ausgangsstoffen betrachtet. Aktuelle Ansätze nutzen Brute-Force-Algorithmen zur Ermittlung der Faktorengewichtungen. Deshalb sind vorberechnete Modelle von Vorteil. Das Training erfolgte mittels gewonnener Messdaten, algorithmisch erzeugter Abweichungen und einem spezifischen, mehrlagigen neuronalen Netz. Die Eingangsdaten sind nach einmaliger Anpassung an das Datenformat fortan ohne weitere Vorverarbeitung nutzbar. Metadaten konnten in Einzelfällen den Messdaten zur Erhöhung der Genauigkeit zugewiesen werden. Die bei klassischen PLS-Verfahren für jeden Messdatensatz notwendigen individuellen Optimierungen entfallen.
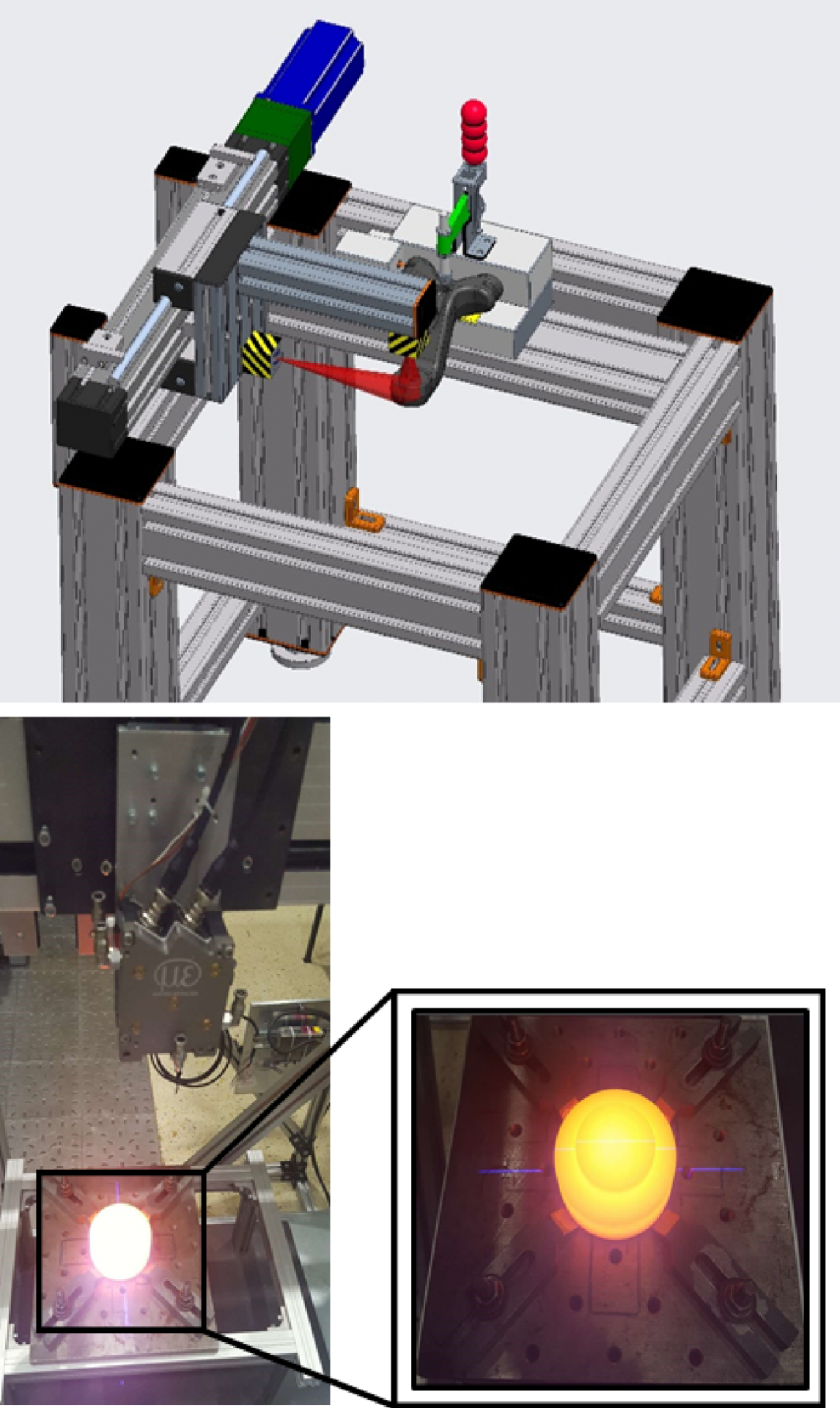
Ziel des Projekts war es, Möglichkeiten für eine messtechnische Bewertung heißer Schmiedeteile während des Produktionstakts aufzuzeigen, um so frühzeitig Formabweichungen (Warmmaße / Geometrie) detektieren zu können
Die digitale Messdatenerfassung ermöglicht es, die Ausschussrate zu minimieren und folglich den Energie- und Materialeinsatz, sowie die damit verbundenen Kosten zu senken. Dank einer Kombination von optischer und laserbasierender Datenerfassung unter herkömmlichen Arbeits- und Umgebungsbedingungen in der Schmiedeindustrie wird eine schnelle Erkennung von fehlerhaften Schmiedeteilen ermöglicht. In Folge des Einsatzes derartiger Datenerfassung wird eine präzise Analyse der Fehlerursache mit einer umgehenden Korrektur dieser realisierbar. Mittels dieser Vorgehensweise steht einem nachhaltigen Produktionsprozess in einem modernen Produktionsumfeld der Schmiedeindustrie nichts im Wege.
Die Methode wurde im Projekt erfolgreich bei der Vermessung von 3D-Geometrien im Temperaturbereich bis 1200°C eingesetzt, wobei es gelang Messdaten entlang der Abkühlkurve zu erfassen.
Der Einsatz der digitalen Messdatenerfassung im genannten Hochtemperaturbereich ermöglicht neben der Steigerung des Materialausnutzungskoeffizienten, eine Senkung der Ausschussrate, sowie die Einsparung wichtiger Ressourcen. Bedingt durch die schnelle Datenerfassung und der damit einhergehenden Korrektur ist außerdem eine Steigerung der Produktivität möglich.
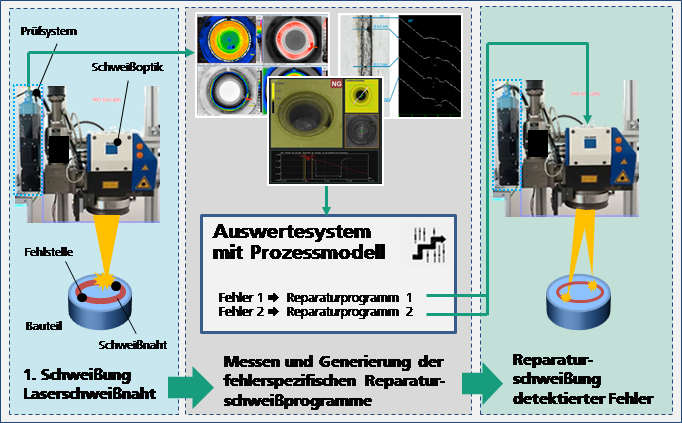
Mit dem Forschungsvorhaben soll, zusammen mit der Firma a.i.m. all in metal GmbH, ein neues Fertigungskonzept entwickelt und umgesetzt werden. Da das Entstehen von Schweißnahtfehlern in einer Serienproduktion durch keinerlei Maßnahmen je völlig ausgeschlossen werden kann, beinhaltet dieses Konzept die automatische Detektion möglicher Imperfektionen mittels einer zerstörungsfreien Prüfung und die nachfolgende Reparatur der Schweißnahtfehler noch innerhalb der Serienanlage durch eine automatische, selbstparametrisierende Fehlerreparaturstrategie.
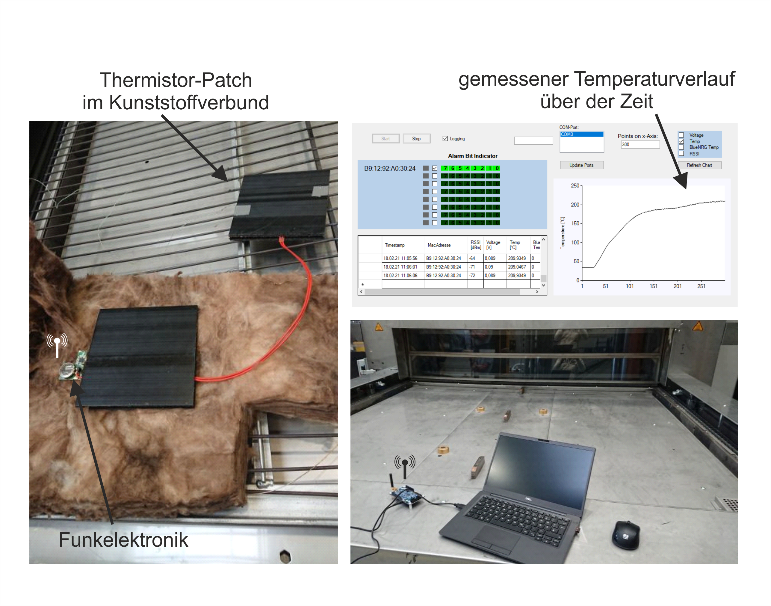
Im Bereich Leichtbau eröffnet die Sensorintegration vollkommen neuartige Möglichkeiten der automatischen Datenerfassung. Dabei können zwei grundlegende Technologien für die Integration von Sensoren in Bauteile unterschieden werden. Zum einen die Erzeugung sensorischer Funktionen/Strukturen durch Funktionsdruck während des Fertigungsprozesses. Zum anderen die Integration von diskreten, vorgefertigten Sensoren während des Fertigungsprozesses. Das Ziel des institutionsübergreifenden Projektes war, im Projektverlauf auf die Integration vorgefertigter Sensorelemente abzuzielen. Der wichtigste zu überwachende Prozessparameter ist die Erfassung der Temperatur während des Aufheizens der Zuschnitte im Umluftofen und während des Umformens der Organobleche und das möglichst ohne eine aufwändige Verdrahtung vor dem Prozess vornehmen zu müssen. Dafür wurde im Projektverlauf eine batteriebetriebene Elektronik und Bluetooth® Low Energy-Microcontroller mit angepasstem Funkprotokoll entworfen, die einen auf den Zuschnitten eingebrachten Hochtemperaturthermistoren ausliest und die Daten entweder an eine Android Applikation oder an eine Computer GUI (betrieben mit Bluetooth® Gateway) übermittelt. Die so gewonnenen Messdaten dienen dazu, prozessrelevante Schwankungen zu detektieren und dem entsprechenden Regelkreis in der Anlagentechnik zu übermitteln. So werden Temperatureinflüsse während des Herstellprozesses minimiert und optimiert.
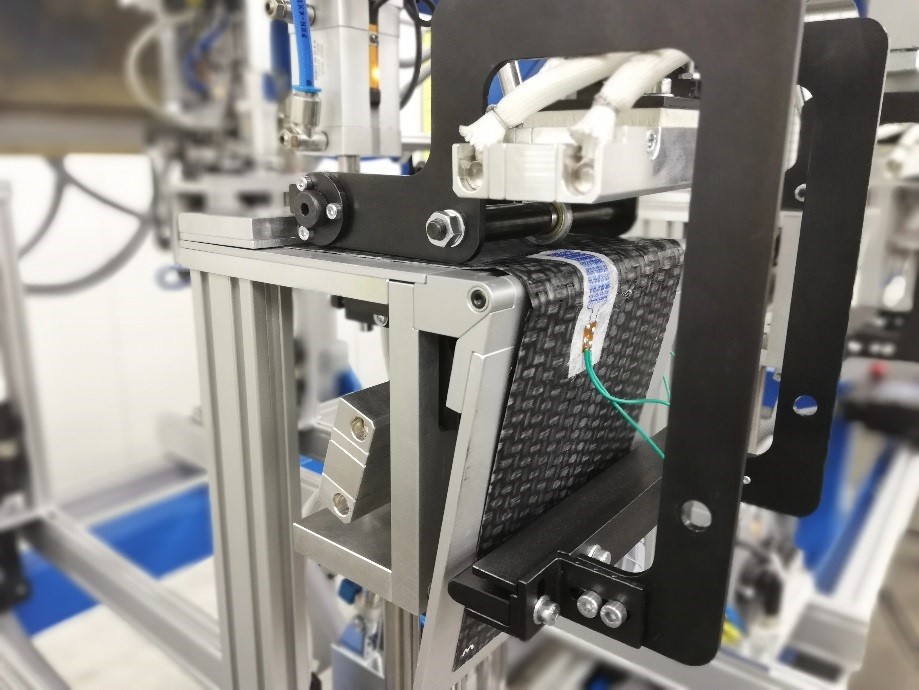
Strukturbauteile für automobile Anwendungen werden in zunehmendem Maße aus thermoplastischen Faserhalbzeugen im Pressverfahren hergestellt. Die Kombination aus UD-Halbzeugen, Organoblechen, fließfähigen GMT-Halbzeugen sowie funktionalen Metalllagen erlaubt dabei die Umsetzung von belastungsgerechten und funktionalen Bauteilen hoher Komplexität. Bei der Verarbeitung der verschiedenen Halbzeugmaterialien im Pressprozess ist ein geregeltes Temperatur- und Druckverhalten zwingend erforderlich, um hohen Bauteilqualitäten sicherzustellen sowie thermische Materialschädigung zu vermeiden. Ziel des Vorhabens ist die Entwicklung eines Systems zur Prozessdatenerfassung während der Herstellung von Strukturbauteilen aus thermoplastischen Faserhalbzeugen im Pressprozess.
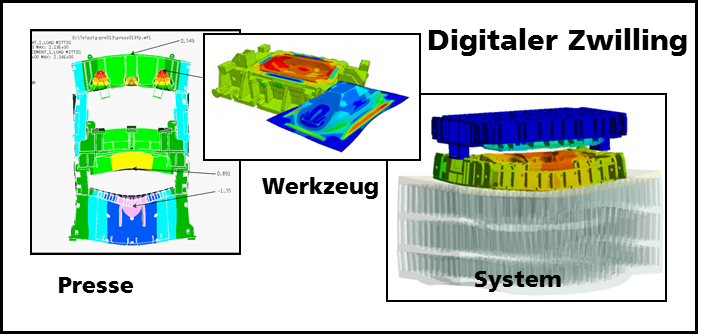
Der Werkzeugeinarbeitungsprozess erfolgt spezifisch und zeitintensiv für jede Kombination aus Umformmaschine und Werkzeug in einer hochgradig manuellen und erfahrungsbasierten Weise. Über die Verwendung gemeinsamer Digitaler Zwillinge sowohl für das Verhalten der Umformmaschine, des Werkzeuges als auch des Umformprozesses wird der Entstehungsprozess weiter qualifiziert und eine Reduktion des Aufwandes ermöglicht. Das Projekt zielt damit auf die ganzheitliche Betrachtung der Umformung und den Einbezug der relevanten elasto-mechanischen Zusammenhänge in die Umformsimulation sowie die generelle Bereitstellung von das Maschinenverhalten charakterisierenden Modellierungsansätzen. Weiterhin lässt ein entsprechend abgeglichener Digitaler Zwilling sich in anschließenden Domänen wie Prozessüberwachung, Qualitätssicherung oder Instandhaltung einsetzen.
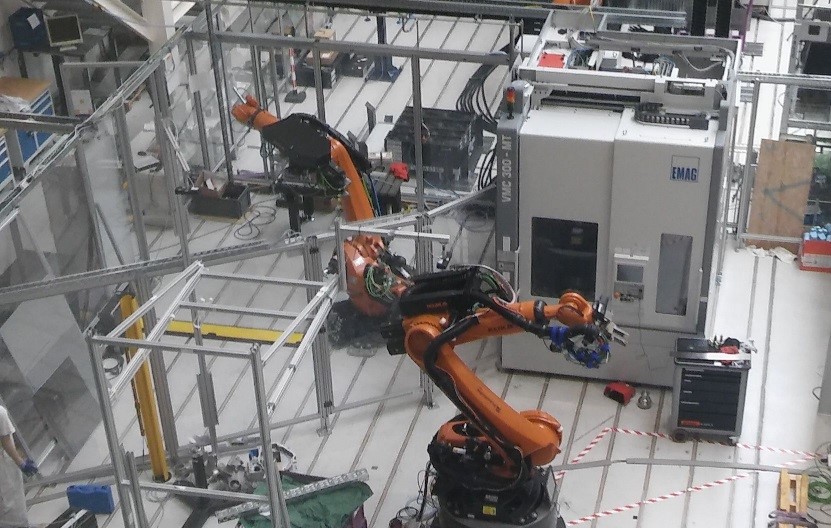
Industrieroboter gewinnen als wirtschaftliche Alternative in der Fertigung zunehmend an Bedeutung. Durch ihren konstruktiven Aufbau besitzen sie jedoch auch verschiedene Nachteile wie eine vergleichsweise hohe statische und dynamische Nachgiebigkeit und eine signifikante Posenabhängigkeit ihrer Eigenschaften. So kommt es beispielsweise aufgrund des trägheitselastischen Verhaltens bei Beschleunigungsvorgängen (z.B. Kurvenfahrten) zu ungewollten Bahnabweichungen.
Im Rahmen des Projektes wurden deshalb neuartige Ansätze für die direkte Messung der Posenbahn (TCP-Bahn) von Bewegungssystemen und insbesondere Industrierobotern theoretisch untersucht und Grundlagen für die Weiterentwicklung eines erfolgsversprechenden Ansatzes geschaffen. Der neuartige Ansatz für ein direktes TCP-Messsystem hat das Potenzial, die wahre TCP-Bahn bei Bewegungen unter Beschleunigungseinfluss direkt zu messen und kann damit zusätzlich zu den inhärenten Messsystemen mit in die Antriebsregelkreise integriert werden. Darüber hinausgehend kann das Messsystem zur effizienten Kalibrierung und zur Identifikation von Modellparametern für die modellbasierte Fehlerkompensation genutzt werden.
Neben Industrierobotern ist der Einsatz eines derartigen Messsystems insbesondere auch für große Werkzeugmaschinen im Werkzeug- und Formenbau interessant, da diese aufgrund ihrer Dimension und den häufig auftretenden Beschleunigungsvorgängen ebenfalls anfällig für ungewollte Bahnabweichungen sind.
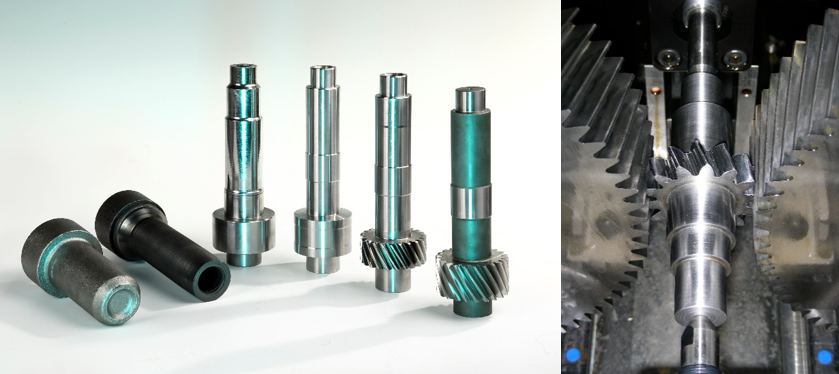
Zielstellung des Teil-Projektes im Rahmen des Leistungszentrums Smart Production and Materials ist die Entwicklung und Erprobung kombinierter Fertigungsfolgen (Umformung und Zerspanung) für rotationssymmetrische Bauteile auf einer Maschine. Basis ist dabei eine umformbasierte Prozesskette für Getriebehohlwellen, wobei speziell die Fertigung der wellenintegrierten Verzahnung auf innovativen Umformprozessen basieren soll.
Im Speziellen sollen die Verzahnungsvorbearbeitung und die Hartfeinbearbeitung auf einer Maschine realisiert und umgesetzt werden, mit der Option für induktive Erwärmungsprozesse (flexibles Erwärmungssystem). Zu realisierende Arbeitsschritte im Projekt sind die Optimierung der umformenden Teilprozesse der Verzahnungsherstellung in den entsprechenden Verzahnungsqualitäten, die konstruktive und bauliche Umsetzung einer kombinierten Umform/Zerspanmaschine beim industriellen Anwender sowie die Entwicklung und Integration einer induktiven Erwärmungseinheit für eine flexible Gestaltung sowohl von Kalt- als auch vor allem Warmumformprozessen zur Verzahnungsherstellung.